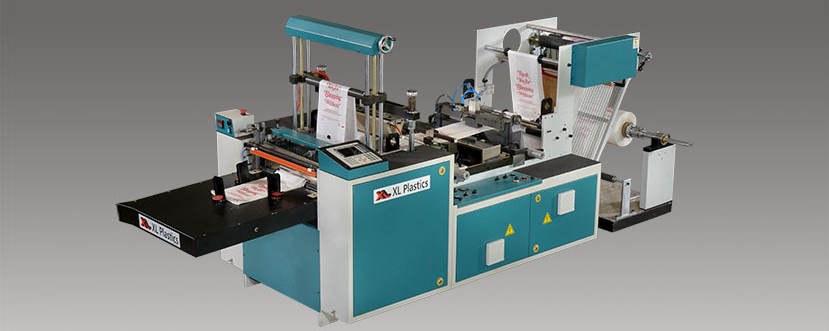
How are Plastic Bags Made?
Plastic bags enjoy their widespread popularity as they are exceptionally versatile and durable in terms of use. Plastic, otherwise known as poly bags, are extremely convenient and can be used to store food, carry goods and products, and can be re-used as trash liners or to collect waste, etc. They are especially popular because they are easy to store and can be folded to fit any storage space, making them easily accessible when required.
Due to its varied number of uses as well as its durable nature, these poly bags can be re-used multiple times. The type of material used to produce these poly bags also allow for easy customization in terms of shape, style, size etc., making them the preferred material for everyday storage needs in various industries.
Based on the type of plastic, the quality and quantity, and the desired use, the type of machine required to produce the bags are determined. While the equipment and material needs may differ based on the factors mentioned above, the basic production process is fairly simple; the only requirement being that it must be completed using the right equipment, in an appropriate environment. Here is an overview of the plastic bag making process to help you gain a better idea of the kind of material and equipment you will need to produce them:
The Extrusion Process
The first step of the plastic bag making process is known as the extrusion process, where an extruder is used to heat polythene plastic resin pellets to a temperature of about 500 degree Fahrenheit. Once the pellets melt, a screw inside the extrusion machine pushes the molten plastic through the machine and into a die that controls the thickness of the product. After which, the molten plastic is supplied with air to create a bubble, to initiate the cooling process. The air is then pinched out and the bubble is flattened to cut the film in the required size which is later wrapped on a spindle.
The Conversion Process
Once the extrusion process is completed, the product is sent to the conversion department for further processing. After the plastic is unwrapped, it is sliced with a heated knife that seals the sides while cutting the plastic sheet into the desired shape or size. Then, special characteristics are added for the completed product. This includes dies that are used to cutout the handles, wheels for production of gussets and various other features are added, those include the logo printing, and addition of seals are taken care of in this step to obtain the finished bag.
Since the process is so simple and highly standardized, thousands of bags can be produced within short periods of time, at cost effective rates. The equipment used to produce these bags are also widely available and can be distinguished based on the type of plastic bag it produces. You can pick from a large variety of plastic processing equipment such as Bottom Seal Bag Machine, Side Seal Bag Machine, Soft Loop and Patch Handle Bag Machine, the T-Shirt Bag Making Machine, along with various other Special Purpose Bag Making Machines to name a few. All you need to do is identify your bag making requirements and needs to select the right equipment. So, if you are looking to purchase a plastic bag making machine, get in touch with us at XL Plastics or call us on call us on +91 265 2830155 and let us help you make a well-informed decision!